With the surge in demand for computational power driven by AI technologies, major manufacturers are developing new high-speed optical module products to meet the rapidly growing market needs. Considering factors such as size, cost, and power consumption, two concepts gaining prominence are Linear-drive Pluggable Optics (LPO) and Co-Packaged Optics (CPO).
Internal Jumper-Type CPO
In CPO switches, minimizing electrical interconnects is essential. The fiber routing from optical engines (including transmitters and receivers) to the switch chassis front panel is unavoidable.
Since optical engines (OEs) are positioned around the ASIC, the distance from each OE to the front panel varies, complicating internal fiber routing within the switch.
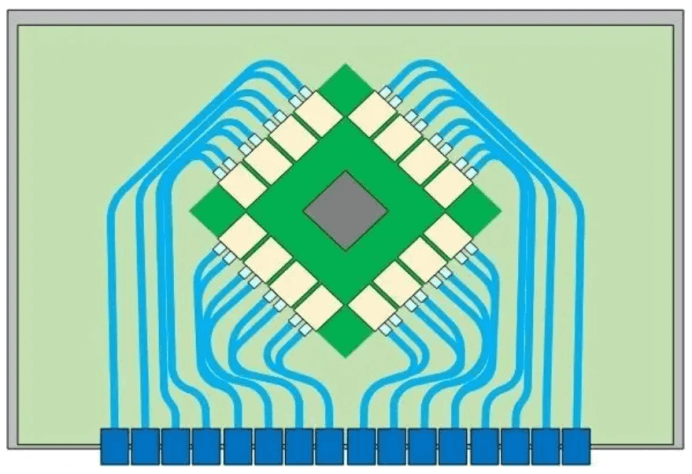
CPO modules, with their multi-channel high-density packaging, require high-precision fiber array (FA), MT, or MPO connectors. However, this specification increases the risk of issues like cracks, poor matching, and long-term performance degradation.
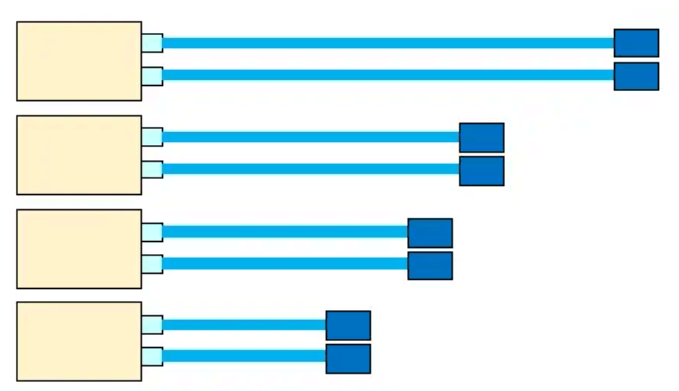
Uneven lengths of high-density patch cords pose challenges for manufacturers and increase the risk of fiber damage during installation, especially for longer patch cords.
Many CPO modules produced using the CPO process use FA-type patch cords for internal fiber routing and pluggable connections. However, some manufacturers explore an alternative approach using flexible backplane materials.
This method routes pure bare fibers on a flexible backplane substrate, resulting in a cleaner and more organized internal fiber layout.
Directly connecting bare fibers reduces connector insertion loss and avoids issues related to damaged end faces, dust, and incomplete matching.
Connector manufacturer SENKO addresses these challenges by employing an intermediate board or board-mounted optical interconnect solution.
Using a single length of FA patch cord for coupling with OEs, the other end of the patch cord connects to the front panel using customized fiber adapters (flanges) in a plug-and-play manner.
While this approach introduces additional fiber end-face connections, it significantly improves maintainability, repairability, and cost savings.
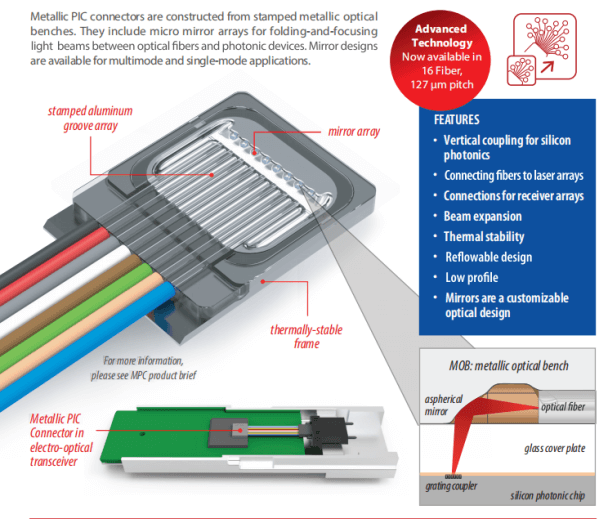
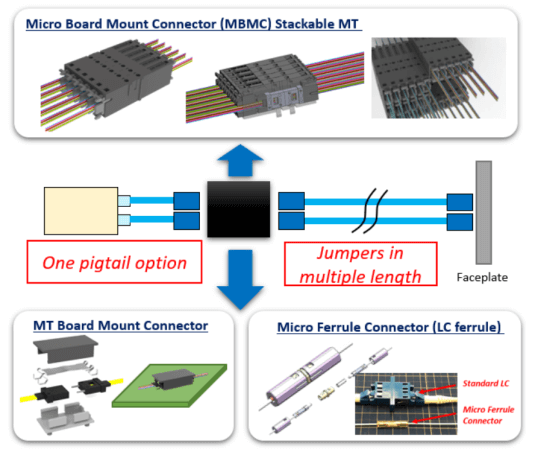
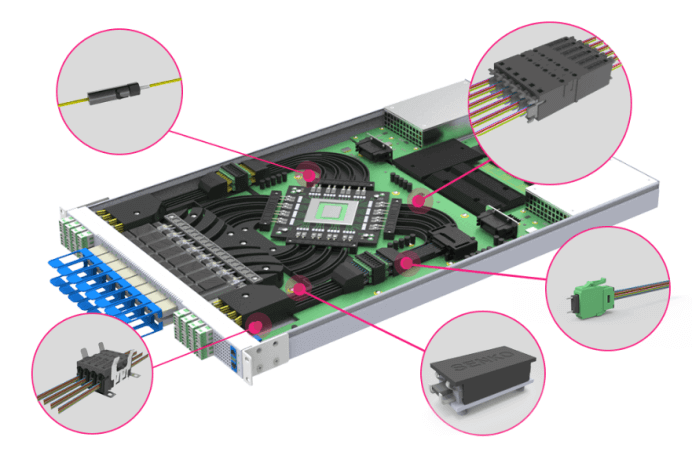
Optical Backplane Approach
Currently, in the production of high-speed optical modules using Co-Packaged Optics (CPO) technology, the predominant method involves using FA-type patch cords for internal fiber routing and pluggable connections. Additionally, some manufacturers utilize flexible backplane materials as a substrate, installing pure bare fibers on top for routing. Clearly, this approach, which employs end-to-end port connections, results in a cleaner and more organized internal module layout. Furthermore, direct connection using bare fibers reduces connector insertion loss and avoids issues related to damaged end faces, dust, and incomplete matching.
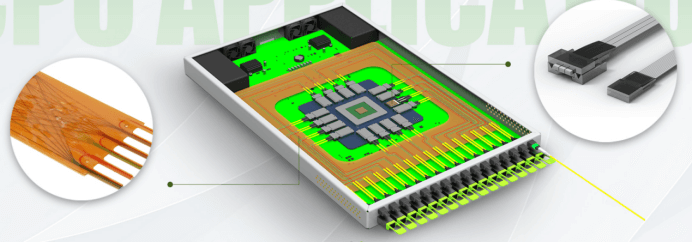
Due to the advantages of the fiber flexible backplane approach, FiberMall has been an early adopter of this technique, implementing it in large-scale data centers with the aim of replacing jumper plugging and alleviating cable clutter. However, this technology still needs to address long-term stability and resilience to external environmental interference. Additionally, standardization of port-to-port interfaces and testing metrics across different manufacturers remains a challenge.
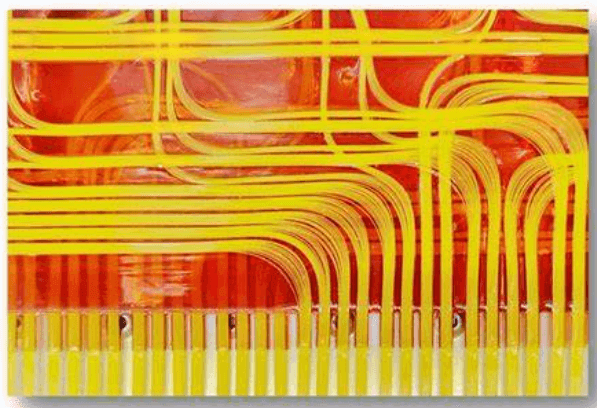
Conclusion
While CPO technology holds significant potential for enhancing data center interconnect performance, it also introduces complexities in fiber routing. Industry solutions, such as SENKO’s intermediate board or board-mounted optical interconnect method and the use of flexible backplane materials with bare fibers, offer advantages in reducing losses and simplifying wiring. However, achieving widespread adoption requires overcoming challenges related to long-term stability and standardization.
Related Products:
-
QSFP112-400G-LR4 400G QSFP112 LR4 PAM4 CWDM 10km Duplex LC SMF FEC Optical Transceiver Module $1500.00
-
QSFP112-400G-FR4 400G QSFP112 FR4 PAM4 CWDM 2km Duplex LC SMF FEC Optical Transceiver Module $750.00
-
QSFP112-400G-DR4 400G QSFP112 DR4 PAM4 1310nm 500m MTP/MPO-12 with KP4 FEC Optical Transceiver Module $650.00
-
QSFP112-400G-SR4 400G QSFP112 SR4 PAM4 850nm 100m MTP/MPO-12 OM3 FEC Optical Transceiver Module $450.00
-
QSFP56-200G-SR4M 200G QSFP56 SR4 PAM4 850nm 100m MTP/MPO APC OM3 FEC Optical Transceiver Module $139.00
-
QSFP56-200G-FR4S 200G QSFP56 FR4 PAM4 CWDM4 2km LC SMF FEC Optical Transceiver Module $650.00