Fast and dependable connectivity is crucial in the current world, where information is everything. A Duplex LC connector is among the many components that make fiber optic networks possible. For its small size and firm performance, it has become widely used in telecommunications and data center applications. This article will discuss what you need to know about this connector, such as its design, how it works, and the benefits attached to using it. Understanding these things will give readers a clue as to why Duplex LC connectors are preferred over other types when it comes to ensuring a continuous flow of large amounts of data through modern fiber optic systems.
What is a Duplex LC Connector?
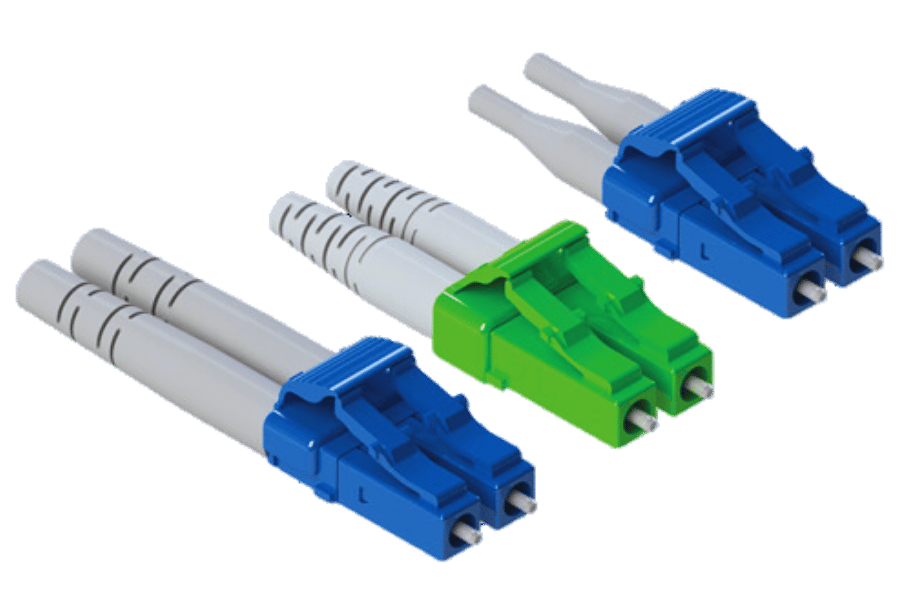
Definition of a Duplex LC Connector
A duplex LC connector is a fiber optic connector that links two optical fibers together in one unit. The “LC” stands for “Lucent Connector,” which is named after the company that created it. The word “duplex” means that this connector has two fibers in one clip, allowing bidirectional communication simultaneously. It is a compact form factor connector with a 1.25mm ferrule and push-pull latching mechanism for easy handling and space-saving. The connector is used with multimode duplex fiber optic cables. This Duplex LC Connector finds its use in places where there are many networks packed together because it supports fast data transfer rates, thus becoming an essential part of any modern-day fiber optics network.
Components of a Duplex LC Connector
- Ferrule: Duplex LC connectors use two ferrules, each with a 1.25mm diameter, to help direct and stabilize optical fibers.
- Body: A small plastic shell protects the inside of the connector including the ferrules from external damage while still keeping them in place.
- Latch: Easily operated by pushing or pulling, this latching system enables users to quickly connect or disconnect connectors in crowded network cabinets with limited space.
- Boot: At the end of the connector, there is a boot that safeguards fragile fiber optic cables by reducing strain on individual strands and thus prolonging their life spans.
- Clip: These clips fasten double connectors together so that they do not come apart when arranged side by side as part of a duplex assembly.
All these parts cooperate to guarantee the stable connection required for transmitting data at high speeds over fiber optic networks.
Why Use a Duplex LC Connector?
There are various reasons why the Duplex LC connector is preferred in modern fiber optic networks. One, it has a small design, making it perfect for crowded spaces where other connectors cannot fit many connections. Two, this type of connector offers superior performance that guarantees low insertion loss and high return loss, which are essential in preserving signal integrity when transmitting data at high speeds. Third, its latch system is designed so that users can easily connect or disconnect with minimum effort, thereby reducing installation time significantly as well as maintenance hours spent on-site. Fourthly, this component supports bi-directional communication, allowing two-way traffic simultaneously through one connection, hence double data transfer capacity over a single link. All these qualities make the duplex LC connectors indispensable elements of today’s fast-paced, highly populated networks.
How Does a Duplex LC Connector Work?
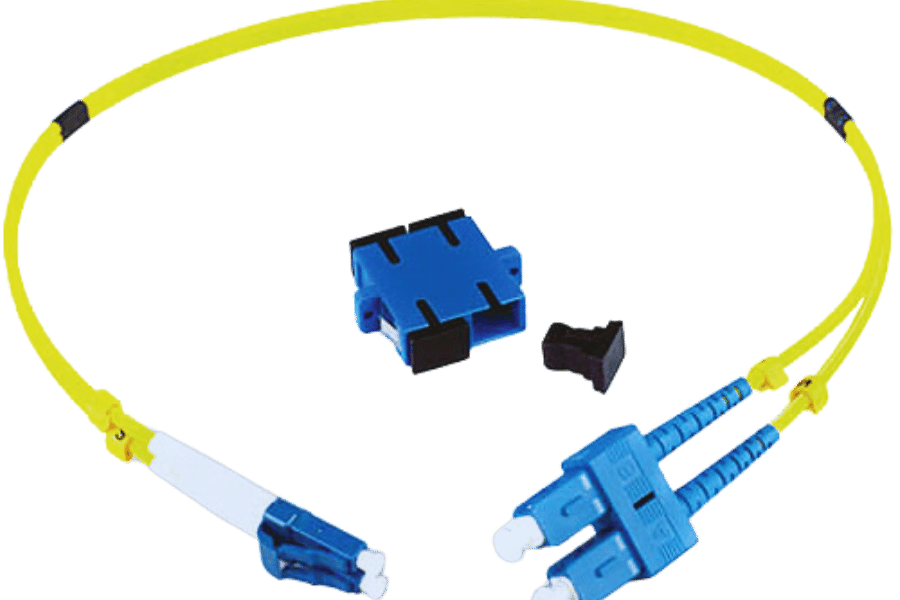
The Role of Fiber in Connectivity
Fiber-optic technology is critical in modern connectivity because it can send data over long distances without loss and interference. The light signals used to transmit this information move through the center of the cable, which is made up of very thin strands of glass or plastic fibers that can transfer data at breakneck speeds. Unlike copper wires, using light instead of electricity creates more bandwidth and higher data rates. In addition, fibers are not easily affected by electromagnetic interferences, thus making sure that there is always a steady connection. Moreover, network reliability may be improved by employing OFNP multimode fiber. Therefore, high-speed networks cannot do without fiber optic technology, which supports various applications such as internet data transfer and telecommunications.
Mechanism of LC Ferrules
In fiber optic connectors, LC ferrules are an essential part because they align optical fibers very accurately, thus optimizing the way signals are transmitted. They are usually made from ceramic or stainless steel with an ultra-precise diameter hole that fits around the fiber core. The key role played by an LC ferrule is to hold a fiber securely without causing any insertion loss and reflection simultaneously. When making connections, these ferrules bring together both cores of the fibers in such a way that allows light to pass through efficiently while still preserving signal integrity for data communication. Such accuracy in alignment helps reduce signal deterioration, making it possible for one to achieve high-speed performance when transmitting data over networks.
Singlemode vs. Multimode Operations
Optical fibers are classified in terms of single mode and multimode, depending on their core size and the principle of transmitting light through them. Duplex multimode fiber optic cables are usually used for short distances.
The small diameter of single-mode fiber cores only allows one light mode to propagate, which is typically about nine micrometers in size. This pathway reduces signal distortion and enables higher bandwidth data transmission over long distances. Single mode is best suited for high-speed internet connections or communication links spanning many miles.
Multimode fibers have larger core diameters – commonly 50 or 62.5 micrometers – permitting multiple light modes to travel simultaneously. This causes modal dispersion, which limits effective distance and bandwidth utilization. For instance, these types work well when connecting different devices located in the same building but not further apart than several kilometers within a metropolitan area network (MAN).
To summarize it all up, single-mode fiber works great with long-haul applications requiring high bandwidths, while multi-mode fibers excel at cost-effective short-range connectivity solutions that meet specific needs.
How to Choose the Right Duplex LC Connector?
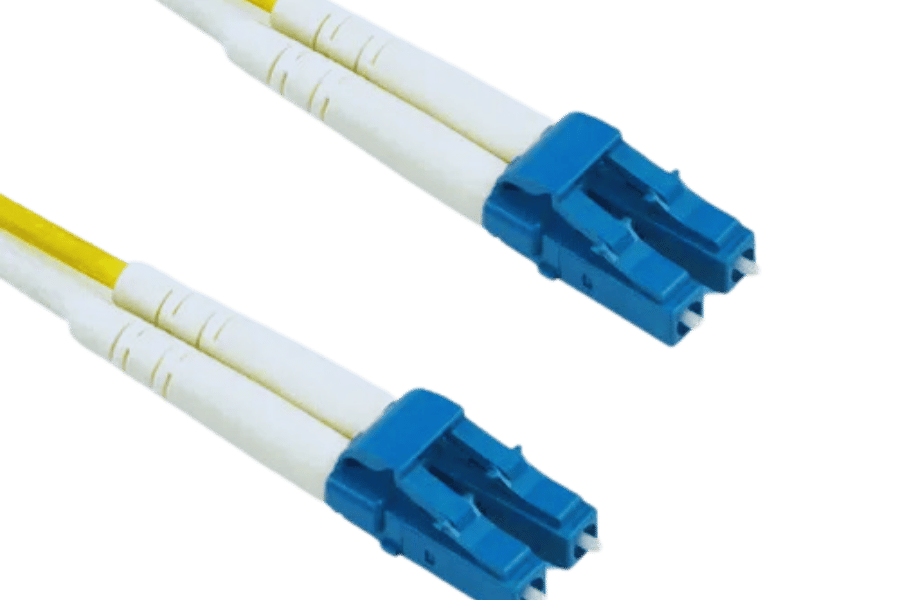
Considerations for Multimode Duplex
When opting for the best duplex LC connector for multi-mode fiber applications, one must consider a number of essential elements.
- Core Diameter and Compatibility: Ensure that you choose a connector that is compatible with the specific core diameter of the multi-mode fiber being used, which is usually 50 or 62.5 micrometers. This will help align them correctly and optimize signal performance.
- Insertion Loss and Return Loss: Choose connectors with low insertion loss values and high return loss figures to minimize signal attenuation and reflection, which can adversely affect network performance.
- Application Environment: Take into account where it will be installed, such as indoor vs. outdoor, data center vs. office space, and then select accordingly. It should be designed suitably based on the environment in order to last longer while remaining dependable at all times.
- Connector Type & Polarity: Ensure that this Duplex LC Connector matches the required connector types and polarities (A-to-B, A-to-A) within your network configuration to ensure proper connectivity and signal flow throughout.
- Performance Standards: Always go for those connectors that meet industry standards such as TIA/EIA or ISO/IEC because they are guaranteed to be of good quality besides being compatible with existing infrastructure; in most cases, these requirements are met by Fiber optic LC connectors since they often fulfill these standards.
By considering each one of these aspects carefully you will end up with a suitable choice for Duplex LC Connectors fitting perfectly into your application needs over multi-mode fibers thus ensuring efficient and reliable data transmission.
Plenum vs. Non-Plenum Cables
When selecting plenum or non-plenum cables, it is important to know the uses and regulations. Plenum wires are made for use in plenum spaces in buildings. They have a special fire-resistant coating and give off less smoke and poisonous gas when they burn than other kinds of cable would. This means that they can be used where strict building codes limit air circulation.
On the other hand, non-plenum cables (also known as riser cables) do not require such stringent fire resistance properties as their counterparts do. They tend to be cheaper and more suitable for vertical runs between floors or in-wall installations where plenum-rated materials are unnecessary. In such cases, duplex fiber connectors may be considered.
In summary, if you are working near air handling systems or within a plenum area, then it’s important to use plenum-rated cables, which will help meet safety standards and regulations. For all other areas outside those mentioned above, riser cable is an affordable alternative that still meets most requirements; however, always refer back to local building codes together with guidelines so as not to breach any safety rules.
Understanding OM1, OM3, and Other Ratings
To compare the ratings of OM1, OM3 and other multimode fibers, it is important that you should have knowledge about their performance characteristics and where they are applicable. The first standard, which is colored orange (OM1 fiber), can support LED-sourced data rates of up to 1GB/s over a distance of 300 meters. It can be used in applications with shorter distance demands since it is less demanding.
While using VCSEL sources, OM3 fiber – usually aqua in color – supports 10GB/s over distances up to 300 meters; this represents a significant improvement over OM1. For this reason, it has been optimized for high-speed data transmission and finds common use in data centers as well as enterprise networks.
Supplementary ratings like the equally colored code named OM4 also enhance its abilities by supporting transmissions of 10 GB/s upto 550m or even 100 Gbps at reduced distances which gives more bandwidth for demanding applications.
On the whole, therefore, each multi-mode fiber rating covers different speeds and distances. Still, when compared to OM1, those aspects are very much improved by both OM3, especially with regards to high-speed networks, where performance matters most, and it would be expected that they would be designed for such purposes as this one here. Therefore, depending on what your network requires specifically in terms of speed and distance coverage, choose appropriately among these options available: OM4, being the latest, offers greater bandwidth capacity than any other type while still ensuring signal integrity remains intact throughout communication links between devices connected via optic cable systems within an organization’s premises or campus area network (CAN).
What are the Advantages of Using LC Connectors?
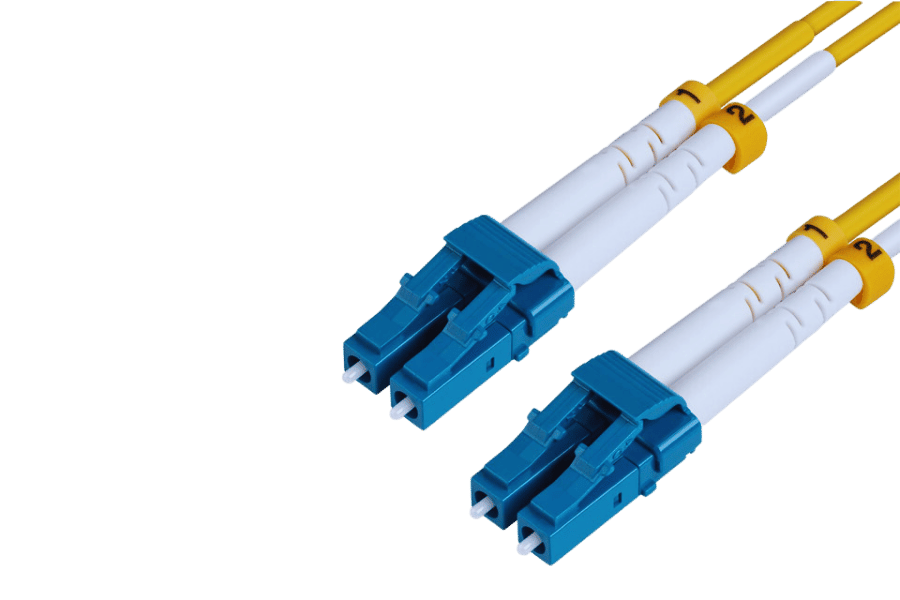
High-Density Connectivity
LC connectors are famous for their dense connectivity, which increases the number of fiber terminations per area. This is done using a smaller design than other connectors like SC or ST. LC connectors have a small size that allows for better space utilization, thereby making it possible to handle many fibers without using many racks as required by bulkier types. Furthermore, LC connectors are often sold in duplex form, where two fibers can terminate on one connector body, thus increasing its density even further. Such features make LC connectors very useful in places with restricted areas, such as data centers and telecom rooms, where efficient use of space is important.
Low Loss Fiber Optics
Ensuring the integrity of the signal and reducing attenuation over long distances can only be achieved using low-loss fiber optics. The phrase “low loss” refers to a lower optic fiber loss measured in decibels per kilometer (dB/km), which is vital for maintaining high-performance transmission in fiber optic networks. Several things need to be considered:
- Material Purity: Fiber optics made from high-quality glass or plastic materials greatly minimize impurities that scatter or absorb light hence lowering signal loss.
- Quality of Core Cladding: The core-clad interface must be well designed to scatter as little light as possible, thereby reducing reflection that leads to overall low-level signaling.
- Wavelength Optimization: For this to happen, it has been realized that there should be particular wavelengths at which these devices should operate best (commonly 850 nm for multimode and 1310 nm or 1550 nm for single mode) due to their most negligible attenuation with light.
By observing these aspects closely, low-loss fiber optics can increase data transmission efficiency, making them suitable for modern high-speed networks.
Durability and Longevity
Fiber optic networks that will be strong and last for a long time require engineering them in a number of ways. These are some of the techniques used to make fiber optic cables rugged:
- Coating: Coating is a technique in which fiber optic strands are wrapped with tough materials, which protect fragile glass or plastic fibers from environmental conditions such as moisture, temperature changes, or even mechanical stress.
- Strength Members: Strength members are included within the cable so as to provide extra mechanical support, thus reducing the chances of physical damage and prolonging the cable’s lifetime.
- Testing in different environments: Cables should undergo various ecological tests to enable them to cope with unfavorable surroundings, such as being immersed in water or exposed to ultraviolet rays, among other extreme temperatures.
The focus on robustness ensures that fiber optics have an average working life exceeding twenty-five years, making it one of the most durable systems available today, with low maintenance requirements for reliable performance.
How do you install and maintain duplex LC connectors?
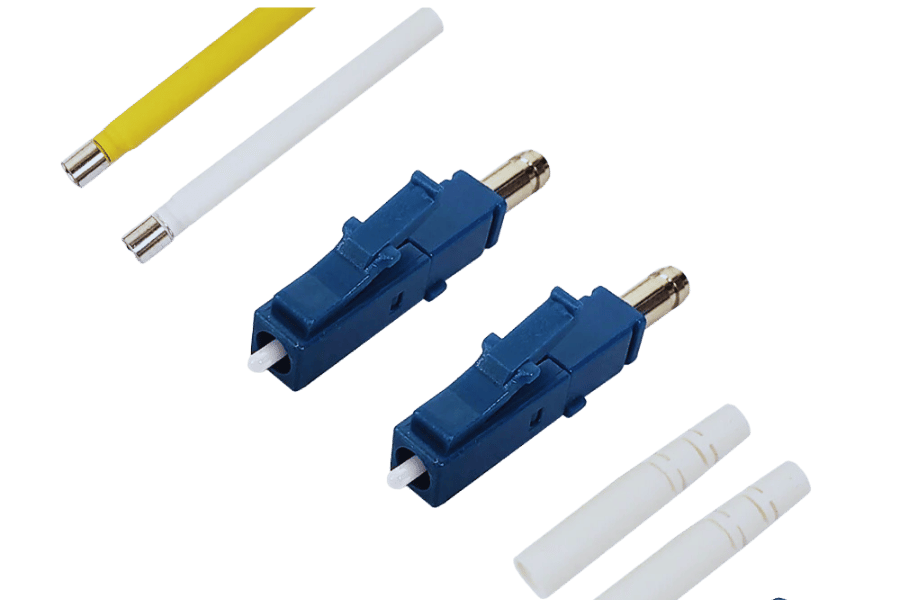
Step-by-Step Installation Guide
Get Ready the Cable: Use a stripping tool to remove about 2-3 cm of the outer coating from the fiber optic cable, being careful not to damage any of its inner fibers.
- Clean the Fiber: Utilize isopropyl alcohol and lint-free wipes to clean off contaminants or dirt that may be present on exposed strands of fibers.
- Cleave the Fiber: Cut at a straight line with a precision cleaver so as to make sure we have an even end face, which guarantees a good quality connection.
- Insert the Fiber: Gently push one end of the cleaved fiber into the rear side duplex LC connector up until it will go in, making certain it aligns properly within the connector housing.
- Crimp the Connector: Fibers within connectors need to be crimped using suitable pressure to stabilize them and ensure reliability during operation after installation.
- Polish The Connector End Face: Lightly rubbing polishing film against the connector’s surface helps remove slight flaws and ensures better transmission of light through it.
- Inspect the Connection: Using a fiber microscope, look at the connector end face for debris or imperfections; if necessary, clean and re-polish the connections.
- Test The Connection: Verify insertion loss and return loss (within allowable limits) by testing connections optical Time Domain Reflectometer (OTDR) or light source power meter combination.
By doing these things, you will ensure that duplex LC connectors are installed securely and efficiently, thus enhancing performance and dependability in any network system using optical fibers.
Using a Duplex 2mm Epoxy Connector Kit
To make use of a Duplex 2mm Epoxy Connector Kit in an effective way, it is necessary to take the following detailed steps:
- Prepare the Fiber: Start by stripping the fiber to expose the cladding, being careful not to damage inner fibers.
- Mix and Apply Epoxy: Follow the manufacturer’s instructions and mix epoxy resin with hardener. Then, apply mixed epoxy to the connector ferrule, insert fiber through the ferrule hole, and ensure that the fiber is coated with epoxy.
- Cure The Epoxy: – Put connector assembly into epoxy curing oven or use a heat gun to cure epoxy as directed by the manufacturer of epoxies; make sure that all parts are correctly cured for good holding strength on fibers.
- Cleave the Fiber: Once cured, use a precision cleaver to cut fiber sticking out from the ferrule so that it creates flat, even ends.
- Polish Connector End Face: – Employ a polishing puck together with a series of polishing films (coarsest to finest) for this process, which is done critically towards achieving low insertion loss performance and high return loss performance; follow instructions given in the kit starting from coarse grit moving progressively towards finer grits.
- Inspect Connector: Use a fiber optic inspection microscope to inspect the polished connector end face; look for scratches, pits, or debris that might affect its functioning, and if necessary, re-polish it.
- Test Connector: – Finally carry out optical testing using Optical Time Domain Reflectometer (OTDR) or light source power meter ensuring connection meets industry standard for insertion loss return loss.
By following these steps one can terminate duplex 2mm epoxy connectors reliably thus ensuring proper operation integrity of their fibre optic network is maintained.
Maintenance Tips for Optimal Performance
To keep your fiber optic network performing at its best, follow these maintenance tips:
- Regular Cleaning: Always clean connectors, adapters and ports regularly with cleaning tools designed for fiber optics such as lint-free wipes and isopropyl alcohol. Foreign materials can cause significant signal loss. Hence, ascertain that your fiber optic lc connector is always clean.
- Visual Inspection: Use a microscope for inspecting all cables and connectors so as to detect potential problems like dust or scratches early enough before they become worse.
- Proper Storage: Store unused cables and connectors in a dust-free environment with their protective caps on to prevent physical damage and contaminants from entering.
- Cable Management: Employ structured cable management techniques that will ensure neatness while avoiding bending too much which can lead to stress related failures besides causing signal losses due to increased attenuation.
- Environmental Control: Ensure that installation sites are free from extreme temperatures fluctuations as well as high humidity levels among other factors known to affect performance. In such conditions, corning optical fiber glass may be more resilient than other types of fibers.
These are some of the things you should do if you want your network stay functional for long without any issues arising. Check duplex fiber optic patch cable connections regularly.
Common Issues and Troubleshooting Tips
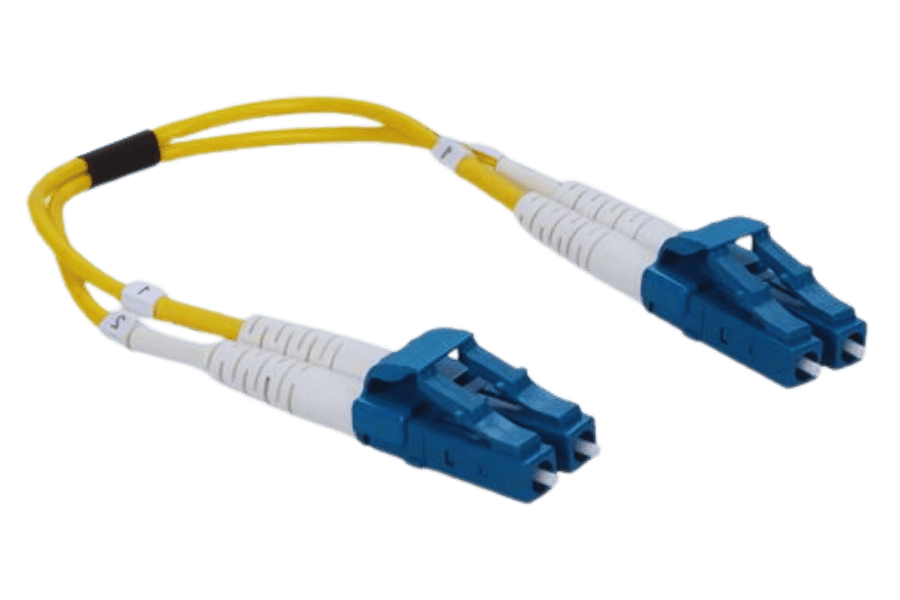
Identifying and Fixing Connector Problems
In fixing connector problems, a methodical approach must be followed. I start by visually examining the cables and connectors for damage or dirt using a microscope for fiber optic inspection. Dust or oil are typical impurities that can seriously affect signal quality. Then, I clean up these connections with suitable cleaning tools meant for fiber optics, like isopropyl alcohol and lint-free wipes, until they are debris-free.
If the problem continues, I employ an Optical Time-Domain Reflectometer (OTDR) to locate faults or breaks along the fiber cable. It’s crucial that you ensure connectors are well mated together and tightly secured because loose ones may result in high insertion and return loss.
There are situations where we may need to re-terminate or replace faulty connectors to bring back good signal performance levels. With this procedure, I am able to quickly find out what went wrong with my connection points and fix it, thus making them work again better than before being attended to, which helps keep up high performance standards for fiber optic networks.
Ensuring Proper Alignment and Connections
To make a fiber optic network properly aligned and connected there are some processes that must be followed carefully. My first step involves checking whether the fiber cores have been aligned correctly or not through the use of an optical fiber visual fault locator or alignment tool. It should be understood that accurate alignment is crucial in minimizing insertion loss and maximizing signal transmission.
The next thing I do is inspect connectors to see if they are clean and free from any dirt particles because small contaminants can lead to significant degradation of signals.
Once connectors are cleaned up and checked, I mate them together with extra care taken so that they can create secure and stable connections. One has to ensure proper seating of these connectors plus engaging locking mechanisms, which will prevent any movement capable of introducing signal errors. Connection testing is also done using an Optical Loss Test Set (OLTS), which measures insertion loss and return loss to verify that they fall within acceptable limits, particularly for systems using corning optical fiberglass.
Therefore, by checking alignment methodically, cleaning connectors, and utilizing accurate testing tools, strong, efficient connections within the fiber optic network are assured. Such keenness guarantees high performance reliability too.
Maintaining Fiber Optic Patch Cable Integrity
To guarantee network dependability and efficiency, it is important to protect the integrity of fiber optic patch cables. Physical damage can be averted by following specific handling procedures at all times. For instance, they should not be bent or twisted beyond their limits or pulled too hard which could result in microbends that lower signal quality. It also means using the right cable management systems, such as protection sleeves designed for bend radiuses, among others, so that physical stress on them is minimized.
Besides, frequent checks are necessary. I personally inspect these cables regularly looking out for any visible wear and tear signs; in case there are any damaged parts detected I replace them immediately because if left unattended they may lead to loss of signals eventually. Cleaning connectors prior to making connections cannot be overemphasized because this step helps prevent contamination, which might degrade the quality of signal transmission otherwise, especially when dealing with fiber optics. Moreover, it is advisable to have with you a fibre optic microscope during inspections so that one can see clearly whether connectors are clean enough or not aligned properly.
By taking care when moving around structured cabling systems like patch cords, etc., checking periodically for faults, cleaning regularly through proper kits(based on alcohol), and testing using laser power meters, we ensure safety and maintain good performance levels throughout our networks made up of these types of cables. Otherwise, everything will fail miserably!
Reference Sources
Frequently Asked Questions (FAQs)
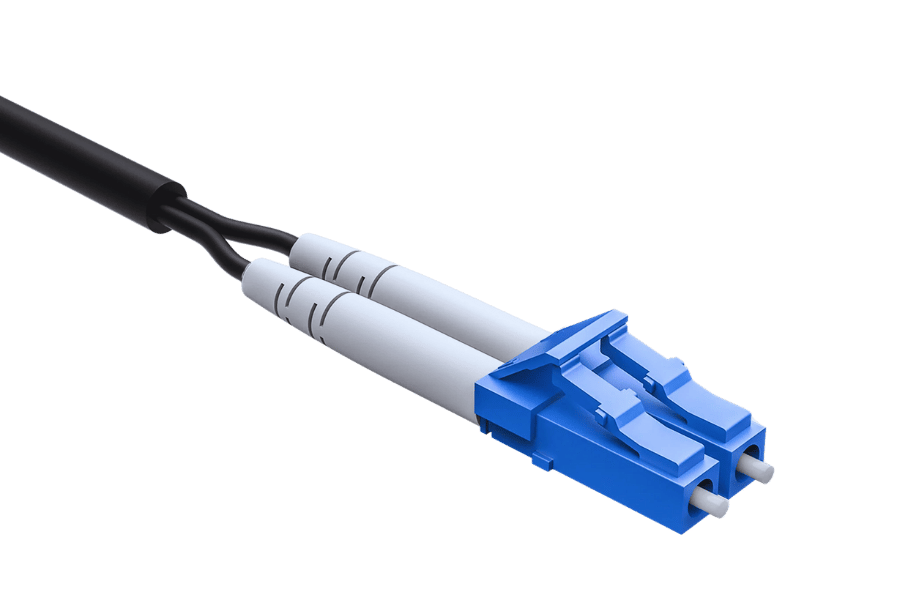
Q: What is a Duplex LC Connector, and why is it considered a go-to solution for fiber networks?
A: A Duplex LC Connector is designed to connect two fiber optic cables using one modular plug. It is widely viewed as the best choice for fiber networks because of its high-density design, low insertion loss, and reliability in single-mode and multimode applications. Multimode options are available with duplex fiber optic cable and patch cable.
Q: What are the critical differences between simplex and duplex fiber connectors?
A: Simplex fibers can only handle one core, which allows data to be transmitted in one direction, while duplex fibers have two cores, which allow data to be transmitted simultaneously in two directions. These types of connectors are used when reliable connectivity with high bandwidth requirements is needed.
Q: What is a plenum duplex fiber patch cable, and where is it used?
A: Plenum duplex fiber patch cords come with plenum-rated jackets that suit use within plenums found in building spaces. These cables meet strict fire safety standards (OFNP rating), which makes them important for commercial installations where compliance with building codes must be met. Such needs require OFNP multimode fibers.
Q: Can you explain the applications of OM3 LC connectors in fiber networks?
A: OM3 LC connectors connect OM3 multimode optical fibers, enabling fast transmission rates of up to 100 Gigabits per second over short distances. Due to their better performance, they are mainly used in data centers and LANs.
Q: What does “LC multimode duplex 2mm epoxy” mean in fiber optics?
A: “LC multimode duplex 2mm epoxy” refers to an LC Fiber Optic Connector for use with multi-mode optical fibers with diameters around 2mm. This connector requires an epoxy adhesive to bond the fiber within the connector body together mechanically to prevent movement between them during regular operation periods. This kind of connector provides good reliability and ease of installation.
Q: What impact does a jacket have on fiber optic cables’ performance?
A: Jackets protect the delicate fiber core against physical damage and environmental elements. Depending on the type of material used for the outer sheath, different levels of protection, flexibility, or fire resistance may be provided, which affects overall cable service life and performance.
Q: Why should one use LC ST duplex fiber patch cables?
A: LC-ST duplex fiber patch cables offer high-density connections and robustness by combining features from LC and ST connectors. They provide compatibility between devices with dissimilar connector types, thus enabling flexibility in complicated network setups.
Q: Why would someone prefer multimode over single-mode fiber optic cables?
A: Multimode allows for many light modes within a short distance, making it suitable for use in areas with high data rates, such as campuses or data centers. It is usually used together with duplex lc fibers to achieve better results. Additionally, multimode cables are cheaper than single-mode ones and are best suited for long hauls since they can transmit signals over longer distances without attenuation.
Q: Why would 1.25mm ceramic ferrule LC connectors be used in fiber networks?
A: 1.25mm ceramic ferrule LC connectors are known for their precision and reliability; they offer good alignment properties while also ensuring minimal signal loss, which makes them ideal for use in high-performance optical networks where stable and efficient data transmission is required.
Q: How do plenum-rated fiber optic cables contribute to network safety?
A: These cables are meant to be installed in plenum spaces, i.e., air circulation areas within buildings, so as to not only meet but exceed fire suppression standards such as OFNP (Optical Fiber Nonconductive Plenum). This reduces the chances of fires breaking out or spreading through them, hence improving overall building security along with everything contained therein, like computer rooms, etc.